Textile finishing is a crucial stage in fabric production, involving a variety of techniques designed to enhance the appearance, texture, performance, and longevity of textiles. In Part 2 of our series, we explore five important textile finishing methods: fabric sizing, brushing, flocking fabric, wrinkle-resistant fabric, and flame-retardant treatment for fabric. Each of these processes serves a specific purpose and is applied based on the intended function and desired properties of the fabric. In this article, we will break down each process in detail, outlining its benefits, methods, precautions, and real-world applications.
Sizing
Fabric sizing is a traditional finishing method in the textile industry, mainly used for the surface treatment of yarns and fabrics to improve their processing performance and the quality of the final product.
Here is a detailed introduction to the textile sizing process:
Purpose of sizing
- Increase strength: Fabric Sizing can increase the strength of the yarn and reduce breakage during weaving.
- Reduce friction: The sizing layer can reduce the friction between yarns or fibers and improve their weavability.
- Protect fibers: The sizing layer can protect fibers from mechanical damage and wear.
- Improve wear resistance: Sizing can improve the wear resistance of the fabric and extend its service life.
- Improve handle: Sizing can improve the handle of the fabric, making it softer or stiffer depending on the desired style.
Sizing methods
- Immersion sizing: Immerse the yarn or fabric in a solution containing sizing agent, and the sizing agent adheres to the surface of the yarn.
- Foam sizing: Use foam to evenly coat the sizing agent on the yarn or fabric.
- Spray sizing: Spray the sizing agent on the yarn or fabric through a spray gun.
- Scraper sizing: Use a scraper to evenly coat the sizing agent on the yarn or fabric.
Sizing steps
- Pretreatment: Clean the yarn or fabric to remove grease, stains, and other impurities.
- Sizing preparation: Select the appropriate sizing agent and ratio according to the required performance.
- Sizing application: Pass the yarn or fabric through the sizing machine to evenly apply the sizing agent to the yarn or fabric.
- Drying: The sized yarn or fabric needs to be dried in a drying oven to fix the sizing agent.
- Post-treatment: The dried yarn or fabric may need to be post-treated, such as removing excess sizing agent and softening treatment.
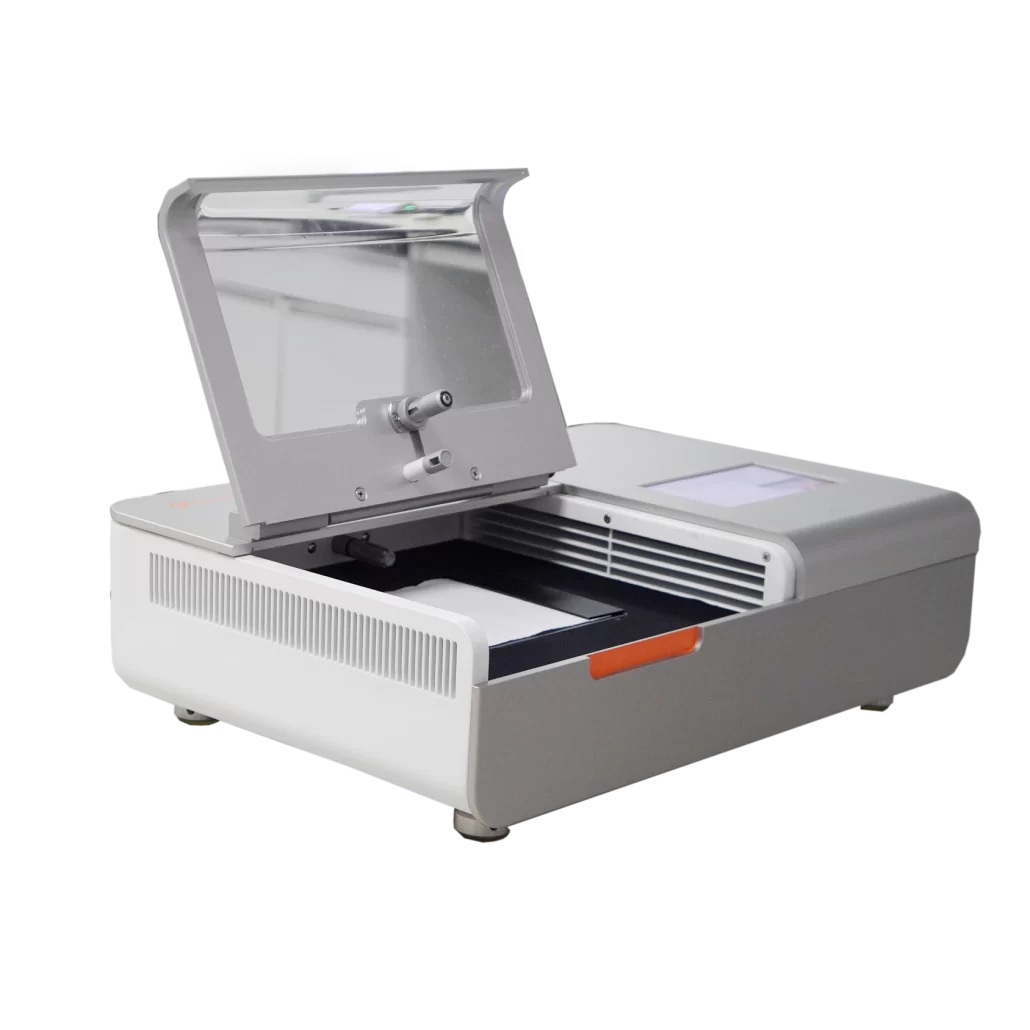
Precautions for sizing
- Sizing agent selection: Select the appropriate sizing agent according to the material of the yarn and the required performance.
- Uniformity of sizing: Ensure that the sizing agent is evenly distributed on the yarn or fabric to avoid local thickening or thinning.
- Drying conditions: Control the drying temperature and time to ensure the proper curing of the sizing agent.
- Environmental protection and safety: Use environmentally friendly sizing agents and ensure that the sizing process is safe and harmless.
- Cost-effectiveness: Consider the cost-effectiveness of the sizing agent and the sizing process to meet the needs of the market and consumers.
Applications of sizing
Sizing finishing is widely used in various textiles, especially those yarns and fabrics that require additional strength and wear resistance during weaving or subsequent processing, such as:
- Warp yarns for weaving: Sizing can improve the strength and wear resistance of warp yarns and reduce breakage.
- Knitting yarns: Sizing can improve the weavability of knitting yarns and increase production efficiency.
- Non-woven fabrics: Sizing can improve the strength and wear resistance of non-woven fabrics.
Sizing is an important means to improve the processing performance and final product quality of textiles. By selecting the appropriate sizing agent and process, the processing performance of yarns and fabrics can be significantly improved. However, the sizing process needs to be precisely controlled to ensure the uniformity and quality of sizing.
Brushing
Brushed finishing is a fabric finishing method that enhances the surface characteristics of the fabric. By brushing, a layer of fine short fluff is created, giving the fabric a soft, warm, and full handle.
The following is a detailed introduction to brushing finishing:
Purpose of brushing
- Improve handle: Make the fabric surface produce fine fluff, and the handle is softer, warmer.
- Increase thickness: Brushing can increase the thickness of the fabric and make it fuller.
- Improve drape: The brushed fabric has better drape and is suitable for making clothing.
- Improve appearance: Brushing can make the fabric surface more uniform and improve its appearance.
- Reduce pilling: Appropriate brushing treatment can reduce the pilling phenomenon of the fabric during use.
Brushing methods
- Wire brush brushing: Use a brushing machine equipped with a wire brush to rub the fabric to produce fluff.
- Sandpaper brushing: Use a sandpaper roller to rub the surface of the fabric, which is suitable for fine brushing effects.
- Carbon brushing: Use a carbon brushing machine to produce fluff through the friction of carbon powder.
- Polishing brushing: Use a polishing roller to polish the surface of the fabric to produce gloss and fluff.
Brushing steps
- Pretreatment: Clean and dry the fabric to ensure the uniformity of the brushing effect.
- Brushing preparation: Select the appropriate brushing equipment and brushes and set the brushing parameters.
- Brushing application: Pass the fabric through the brushing machine for brushing treatment.
- Post-treatment: The brushed fabric may need to be cleaned, dried, and shaped in the post-treatment steps.
Precautions for brushing
- Brushing equipment: Select the appropriate brushing equipment and brushes to obtain the desired brushing effect.
- Brushing parameters: Precisely control the speed, pressure, and time of brushing to ensure the uniformity of the brushing effect.
- Fabric protection: Protect the fabric during the brushing process to avoid damage caused by excessive brushing.
- Environmental protection and safety: Use an environmentally friendly brushing process and ensure that the operation process is safe and harmless.
- Cost-effectiveness: Consider the cost-effectiveness of the brushing process to meet the needs of the market and consumers.
Applications of brushing
Brushing finishing is widely used in various textiles, especially those products that require a soft handle and a full appearance, such as:
- Home textile products: Such as bed sheets, quilt covers, pillowcases, etc., which need to be soft and warm.
- Apparel fabrics: Such as sweaters, sweatshirts, etc., which need a soft and full appearance.
- Decorative items: Such as sofa covers, cushions, etc., which need to be beautiful and comfortable.
Brushing is an important means to improve the handle and appearance of textiles. By precisely controlling the brushing process, the fabric can be endowed with soft, warm, and full characteristics. However, the brushing process needs to be carefully controlled to ensure the consistency of the brushing effect and the high quality of the product.
Flocking
Flocking fabric is a process used to give fabric a velvet-like texture and improved handle. Through the flocking process, short fibers are applied to the fabric surface.
The following is a detailed introduction to textile flocking finishing:
Purpose of flocking
- Increase softness: The surface of the flocked fabric is covered with a layer of short fluff, and the handle is softer and more comfortable.
- Improve appearance: The flocked fabric has a unique appearance, similar to velvet or suede.
- Improve warmth retention: The fluff layer on the surface of the fabric can increase the warmth retention.
- Enhance drape: The flocked fabric usually has better drape and is suitable for making curtains, clothing, etc.
- Provide additional functions: Some flocked fabrics also have moisture absorption, sound absorption, or decorative effects.
Flocking methods
- Mechanical flocking: Use a flocking machine with sharp blades to repeatedly rub the fabric to make the fibers fluff.
- Chemical flocking: Make the fiber surface rough through chemical treatment, and then make the fibers fluff through mechanical friction.
- Thermal flocking: Use high temperature to soften the fibers, and then make the fibers fluff through mechanical action.
- Steam flocking: Use the heat and humidity of steam to expand the fibers, and then make the fibers fluff through mechanical action.
Flocking steps
- Pretreatment: Clean and dry the fabric to ensure the uniformity of the flocking effect.
- Flocking preparation: Select the appropriate flocking equipment and process parameters, such as flocking speed, pressure, and time.
- Flocking application: Pass the fabric through the flocking machine for flocking treatment.
- Post-treatment: The flocked fabric may need to be cleaned, dried, and shaped in the post-treatment steps to fix the fluff and improve the handle.
Precautions for flocking
- Fabric selection: Select the fabric suitable for flocking, such as natural fibers such as cotton, wool, silk, or some synthetic fibers.
- Flocking equipment: Select the appropriate flocking equipment to obtain the desired flocking effect.
- Process parameters: Precisely control the speed, pressure, and time of flocking to ensure the uniformity and quality of the flocking effect.
- Environmental protection and safety: Use an environmentally friendly flocking process and ensure that the operation process is safe and harmless.
- Cost-effectiveness: Consider the cost-effectiveness of the flocking process to meet the needs of the market and consumers.
Applications of flocking
Flocking finishing is widely used in various textiles, especially those products that require a soft handle and a special appearance, such as:
- Home textile products: Such as towels, bathrobes, bed sheets, etc., which need to be soft and absorbent.
- Apparel fabrics: Such as sweatshirts, scarves, etc., which need to be soft and warm.
- Decorative items: Such as sofa covers, curtains, carpets, etc., which need to be beautiful and comfortable.
Flocking is an important means to improve the appearance and handle of textiles. By precisely controlling the flocking process, the fabric can be endowed with a unique texture and style. However, the flocking process needs to be carefully controlled to ensure the consistency of the flocking effect and the high quality of the product.
Wrinkle-Resistant Finishing
Wrinkle-resistant finishing, also known as anti-wrinkle treatment or wrinkle free finish, is a technology used in textile finishing to improve the wrinkle resistance of the fabric. This wrinkle resistant treatment can reduce the wrinkles of the fabric after use and washing, making the clothes easier to care for and the appearance more tidy.
The following is a detailed introduction to wrinkle-resistant textile finishing:
Purpose of wrinkle-resistant finishing
- Reduce wrinkles: Reduce the wrinkles of the fabric caused by folding, pressing, or body movement.
- Easy care: Make the fabric easier to care for and maintain in daily life and improve the convenience of wearing.
- Improve appearance: Keep the clothes smooth and tidy and enhance the overall appearance.
- Increase durability: Reduce the damage to the fabric caused by ironing.
Wrinkle-resistant finishing methods
- Resin finishing: Use synthetic resin as a finishing agent and impart shape stability to the fabric through its cross-linking action on the fibers.
- Liquid ammonia treatment: Use liquid ammonia to pretreat cellulose fibers and then perform resin finishing to enhance the finishing effect.
- Bio-enzyme finishing: Use bio-enzymes to soften cellulose fibers and reduce the binding force between fibers, thereby reducing wrinkles.
- Heat setting: Combine the heat setting process to fix the shape of the fibers and improve the wrinkle resistance of the fabric.
Wrinkle-resistant finishing steps
- Pretreatment: Clean the fabric to remove oil stains and other impurities to prepare for subsequent treatment.
- Application of finishing agent: Immerse the fabric in a solution containing wrinkle-resistant finishing agent or apply the finishing agent by spraying, etc.
- Drying: Dry the fabric to make the finishing agent evenly distributed on the fabric and initially fixed.
- Heat setting: Heat set the fabric under controlled temperature and humidity conditions to form a stable cross-linking of the finishing agent on the fibers.
- Post-treatment: It may include washing to remove unreacted finishing agent, and further drying and softening treatment.
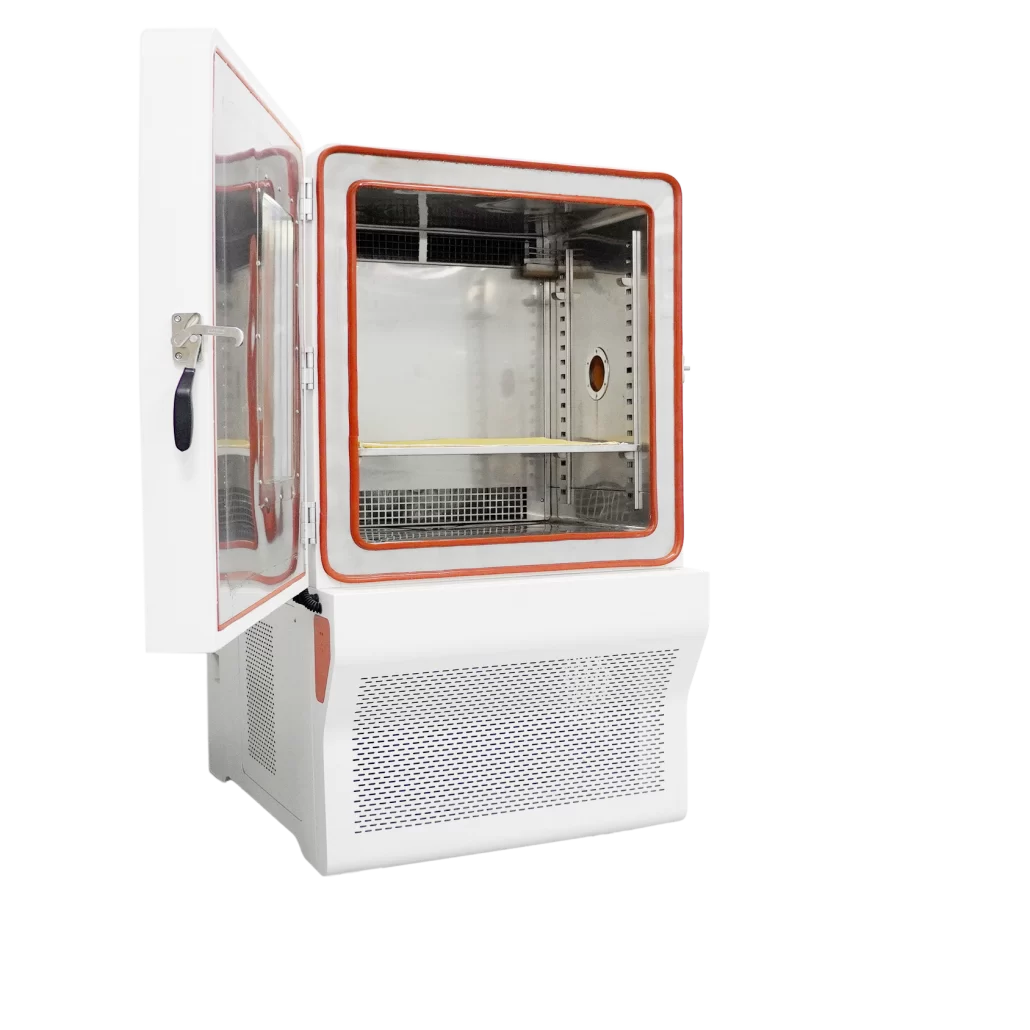
Precautions for wrinkle-resistant finishing
- Finishing agent selection: Select the finishing agent suitable for the fabric type and expected effect.
- Treatment conditions: Precisely control the temperature, time, and pH value during the finishing process to ensure the best effect.
- Safety: Pay attention to the safety of the finishing agent and avoid using substances harmful to the human body.
- Environmental protection considerations: Use environmentally friendly finishing agents and processes to reduce the impact on the environment.
- Cost-effectiveness: Consider the cost-effectiveness of the finishing agent and the process to meet the needs of the market and consumers.
Applications of wrinkle-resistant finishing
Wrinkle-resistant finishing is widely used in various textiles, especially those products with high requirements for appearance flatness, such as:
- Shirts: Reduce the need for ironing and facilitate wearing and care.
- Suits and formal wear: Keep the shape and appearance of the clothes.
- Casual wear: Improve comfort and ease of use.
- Home textile products: Such as bed sheets, curtains, etc., reduce the difficulty of daily maintenance.
Wrinkle-resistant finishing is an important means to improve the practicality and aesthetics of textiles. By precisely controlling the finishing process, the wrinkle resistance of the fabric can be significantly improved to meet the needs of modern fast-paced life. However, the wrinkle-resistant finishing process needs to be carefully controlled to ensure the consistency of the finishing effect and the high quality of the product.
Flame-Retardant Treatment
Flame-retardant treatment is a special textile finishing process used to improve the fire resistance of the fabric, prevent the spread of flames, and thus enhance the safety of the product. This flame retardant treatment for fabric is especially important for textiles that need to meet specific fire safety standards, such as curtains, furniture coverings, children’s clothing, and aircraft interiors.
The following is a detailed introduction to fabric fire retardant treatment:
Purpose of flame-retardant treatment
- Improve safety: Reduce the risk of the fabric being ignited and slow down the spread rate of the flame.
- Meet regulatory requirements: Comply with the fire safety standards for textiles in different countries and regions.
- Protect life and property: Provide additional time for personnel evacuation and property protection in the event of a fire.
Flame-retardant treatment methods
- Chemical method: Bond the flame retardant to the fiber through chemical bonds to impart lasting flame retardant properties to the fabric.
- Coating method: Apply a layer of flame retardant coating on the surface of the fabric to form a protective layer.
- Impregnation method: Immerse the fabric in a flame retardant solution to make the flame retardant penetrate into the fiber interior.
- Foam method: Use foam containing flame retardant to treat the fabric to make the flame retardant evenly distributed.
Flame-retardant treatment steps
- Pretreatment: Clean the fabric to remove oil stains and other impurities to prepare for flame retardant treatment.
- Application of flame retardant: Apply fr treatment for fabricaccording to the selected method.
- Curing: After drying and heat treatment, make the flame retardant solidify on the fabric to form a stable protective layer.
- Post-treatment: It may include washing to remove unbound flame retardant, and further drying and softening treatment.
Precautions for flame-retardant treatment
- Flame retardant selection: Select the flame retardant suitable for the fabric type and expected flame retardant effect.
- Treatment conditions: Precisely control the temperature, time, and pH value of the flame retardant treatment to ensure the best effect.
- Safety: Pay attention to the safety of the flame retardant and avoid using substances harmful to the human body.
- Environmental protection considerations: Use environmentally friendly flame retardants and processes to reduce the impact on the environment.
- Durability: Ensure that the flame retardant effect can be maintained after multiple washings and uses.
- Cost-effectiveness: Consider the cost-effectiveness of the flame retardant and the process to meet the needs of the market and consumers.
Applications of flame-retardant treatment
Flame-retardant treatment is widely used in textile finishing that need to meet specific fire safety standards, such as:
- Curtains and window treatments: Curtains in homes and public places.
- Furniture coverings: Sofa covers, mattresses, etc.
- Children’s clothing: Improve the safety of children’s clothing.
- Aircraft and public transportation interiors: Seats and curtains in airplanes, trains, and buses.
- Medical facilities: Bed sheets, curtains, etc. in hospitals and nursing homes.
Flame-retardant treatment is an important means to improve the safety of textiles. By precisely controlling the finishing process, we can significantly improve the fabric’s fire resistance to meet specific safety standards. However, we must carefully control the flame-retardant treatment process to ensure consistent flame retardant effects and maintain the product’s high quality.
The choice of textile finishing technology depends on the requirements and intended uses of the final product. Different finishing technologies can be used alone or in combination to achieve the best performance and appearance effects.
In conclusion, textile finishing techniques such as sizing, brushing, flocking, wrinkle-resistant finishing, and flame-retardant treatment play essential roles in optimizing the performance and durability of fabrics.
By leveraging the right combination of fabric finishes, manufacturers can ensure their products perform optimally in the market while maintaining competitive advantages. Whether it’s enhancing fabric durability, improving comfort with wrinkle-resistant finishes, or meeting safety standards with flame-retardant treatments, each finishing technique plays a vital role in fabric production.
Understanding these finishing techniques allows producers to cater to the evolving demands of consumers and industries alike, ensuring that their products perform well and remain competitive in the market.
For more information on smart textile testing instruments and fabric finishing techniques, or to obtain professional testing solutions, please contact us!
Email: sales@chivention.com
WhatsApp: +86 180 2511 4082
Linkedin: Chiuvention